Nitriding is one of the most common surface heat treatments, based on the diffusion of nitrogen atoms. It is a very comprehensive method, with numerous advantages, not least of which is its contribution to the overall strength of steel parts. It is available in three variants, which take place in different media: liquid, gaseous and ionic nitriding.
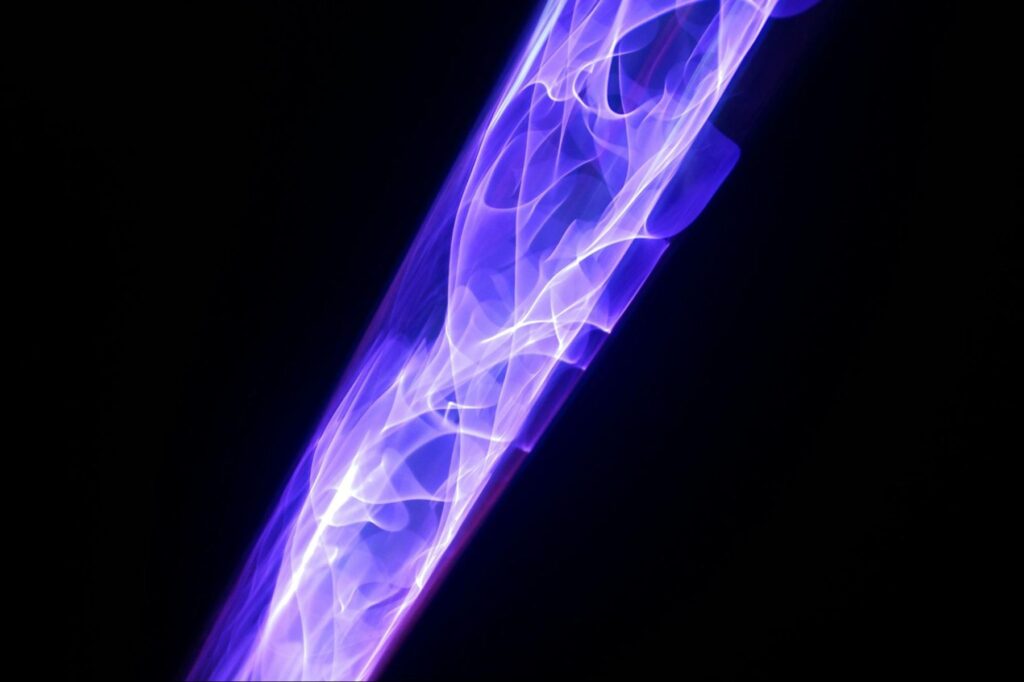
Nitriding: protecting fabricated parts with atomic nitrogen
As the name suggests, nitriding is based on the use of nitrogen. This is a diffusion treatment, during which nitrogen is produced, deposited on the surface of the parts and then diffused inside them. In "nature", this element is only present on a molecular scale (N2), too large to enter the interstices of metal such as steel and protect it. This is why nitriding aims to generateatomic nitrogen (N), which is much more suitable.
This method has become increasingly popular in recent years, as it offers a number of advantages: it takes place in a low-temperature environment, which saves energy and simplifies machining routines; it improves the resistance of parts to wear, fatigue and abrasion; and it causes very little deformation during processing.
By targeting nitrogen diffusion and controlling the depth and formation of the nitrided layer, this treatment process produces a high-performance surface layer that considerably extends the service life and mechanical properties of metal parts, such as gears and tool components, in demanding environments, particularly in industry.
The three main types of nitriding
In practice, nitriding can take place in different media: liquid, gaseous or ionic. While the result of the operation is similar in terms of performance in all three cases, the choice of method depends above all on the parts to be treated, their geometry, the nature of each order and the available budget.
Liquid nitriding: the molten salt bath method
One of the oldest nitriding processes is the salt bath process. This takes place in a liquid environment. In liquid nitriding, salts are heated to between 500 and 600 degrees Celsius. These salts are composed of cyanates(CNO), which then decompose into atomic nitrogen. As a result, metal parts immersed in the salt bath naturally "coat" themselves with a nitrided layer, protecting their entire surface.
Gas nitriding
Gas nitriding relies on the use of a very specific gas, ammonia, NH3. The process involves breaking down this molecule to form atomic nitrogen, which diffuses into the metal part. To achieve this, the environment is heated to between 500 and 600 degrees Celsius in a furnace, generally cylindrical, pot-type or cubic in shape. The parts to be treated are placed in the furnace, and the active gas is injected and maintained at temperature for a predefined time, depending on the desired layer depth.
This method has a variant known as low-pressure gas nitriding. In this case, the atmospheric pressure is lowered from 1,000 millibars to 450 - 500 millibars, enabling less ammonia to be used.
Ion or plasma nitriding
The third type of nitriding takes place in an ionic medium. This is also known as plasma nitriding. This method relies on the formation of N+ ions, which are diffused onto the surface of steel parts to make the nitrogen penetrate. In practice, this technique involves creating a plasma, which both pickles and partly heats the parts. The parts are then placed in an oven, as in the previous situation, and cooled by the forced circulation of neutral gas at the end of the cycle.
This process is particularly well suited to applications requiring high surface hardness and resistance to galling, making it an excellent choice for gears and other highly stressed components.
Each type of nitriding offers unique advantages and is considered in relation to the material, the desired properties and the specific needs of the application. This thermochemical treatment not only enhances the durability and performance of metal parts, but also delivers long-term benefits in terms of mechanical and structural integrity.
Choosing your nitriding process
In practice, all three nitriding processes deliver equally good results in terms of performance. In fact, all three technologies serve the same purpose: to bring nitrogen onto the surface of steel parts to strengthen them and improve, among other things, their resistance to wear. So defining the right method means looking at each order on a case-by-case basis, in the spirit of "customer needs".
For example, in the case of parts with a particular geometry requiring partialtreatment, the ionic method is often the most suitable technology. Thanks to the use of metal covers, it is possible to apply the nitrided layer only to the desired areas of the part surface. However, this method does require a few precautions: if two parts come into contact with each other during treatment, an electric arc forms between them, causing them to melt. For this reason, plasma nitriding is not suitable for bulk batches. If the order calls for a large number of parts to be treated, it is generally preferable to use salt baths or gas nitriding.
In addition, some manufacturers have environmental and energy-saving requirements. In such a configuration, it's best to opt for the gaseous or ionic methods, as the salt baths must be constantly maintained at a working temperature to prevent the salts from solidifying. They therefore consume much more energy than the other two processes if the plant is not in use, where you simply switch on a furnace and then switch it off once the treatment is complete. Liquid nitriding therefore seems more suited to continuous flow production.
What's more, this technique involves analyzing and monitoring baths composed of the chemical species to be monitored. Although this technology is not subject to REACH, the European regulation on the use of chemicals, it does produce polluting waste that needs to be treated. For this reason, Thermi-Lyon has decided to discontinue this process, which we have been using for some fifty years. Conversely, ion nitriding,which takes place in a vacuum, produces no waste or pollution, making it the greenest method.
There are three main nitriding processes: liquid, gaseous and ionic. These three methods deliver excellent results, helping to improve parts' resistance to wear, seizure and fatigue. The choice of the most suitable method actually depends on the nature of the parts to be treated. If only partial treatment is required, plasma nitriding is preferred, whereas in the case of very large batches, gas nitriding is more appropriate. Salt bath nitriding, on the other hand, is well suited to continuous flow production, but is more polluting and therefore cannot meet the requirements of certain clients.