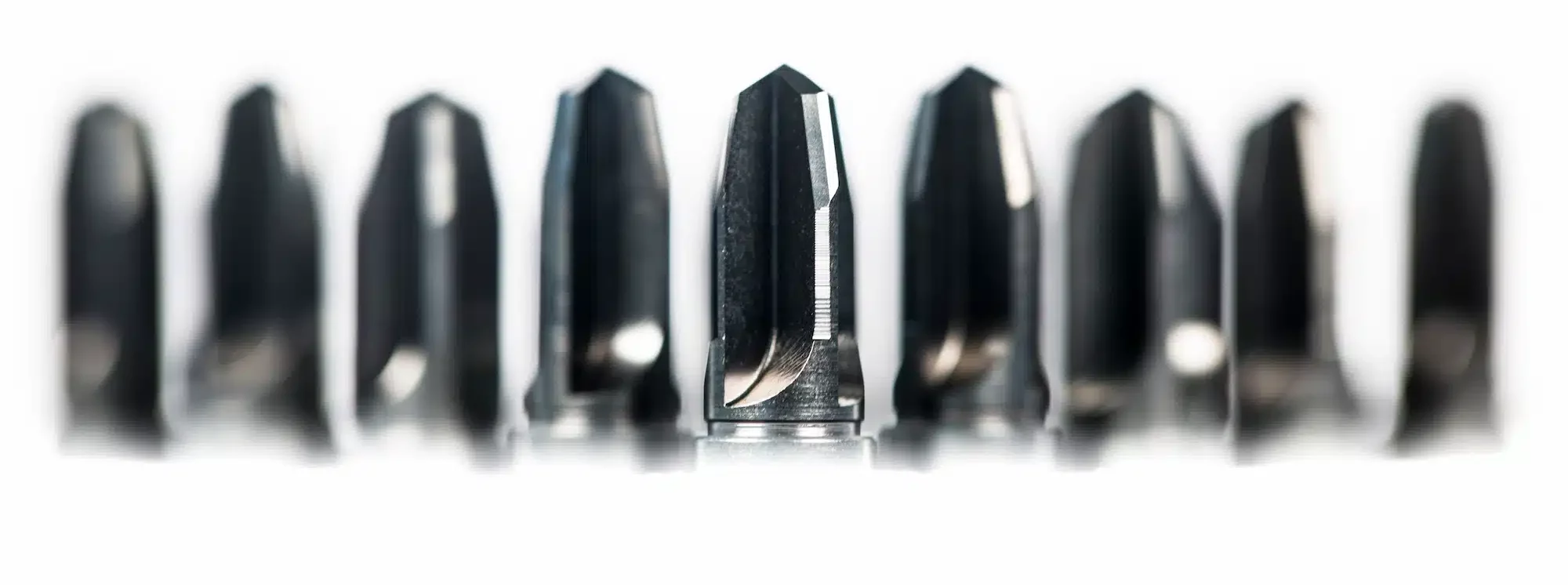
Vacuum deposition
The group's vacuum deposition business was created in 1996 to provide a technically complementary service to heat treatment. The THERMILYON group has been mastering this technology for over 25 years.
Ask for a quoteOur vacuum deposition solutions
Vacuum PVD coatings are surface treatments that can significantly increase part life and wear resistance in a wide variety of environments and fields.
The THERMI-PLATIN website offers a wide range of biocompatible solutions that meet the requirements of the medical sector.
Coatings for tribological applications to improve friction.
Standard vacuum coatings provide performance for versatile use.
DLC coatings produced by PA-CVD enhance the performance of tools and mechanical parts subjected to severe friction, abrasive and adhesive wear, and chemical aggression.
Duplex is the superposition of a thermochemical treatment and a hard coating, with the aim of reinforcing the mechanical strength of the underlay and improving wear resistance on the surface.
Vacuum deposition technologies
Our certifications
ISO 13485 establishes the criteria for the quality management system of an organization providing medical devices and related services in compliance with customer requirements and applicable regulations.
Read moreEN 9100 certification guarantees the quality management system requirements of the ISO 9001 series, and specifies additional definitions and notes for the aerospace and defense industry.
Read moreNADCAP is an accreditation program for aerospace and defense subcontractors, designed to ensure the quality and reliability of products and services. This accreditation focuses on the special processes employed in the manufacture, testing and maintenance of components and systems used in these industries. Within the THERMILYON Group, NADCAP applies only to the special heat treatment process.
Read moreThe ISO 9001 standard, widely recognized throughout the world, helps organizations improve their performance by meeting quality management system requirements and demonstrating a commitment to customer satisfaction.
Read moreSee all our certifications
Our FAQs
Vacuum deposition is a surface treatment used to deposit a material or alloy on a mechanical part.
The use of vacuum technology ensures a perfectly clean, non-polluting process.
It is not subject to REACH legislation.
This process greatly increases resistance to wear, abrasion, friction and corrosion. As a result, component life is greatly extended.
Standard thicknesses are of the order of 3µm and deposition is carried out on finished parts.
PVD is physical vapor deposition. The element to be deposited is obtained by evaporation or sputtering via a physical process. PACVD is plasma-assisted chemical vapor deposition. The element to be deposited is obtained from chemical reactions. Plasma enables this chemical reaction to take place at lower temperatures.
Vacuum deposits are classified into several categories: anti-wear, friction, decorative and biocompatibility. The applications are therefore very varied: automotive components, aerospace, tooling, cutting tools, medical devices, decorative parts...
The deposition method depends above all on the nature of the coating to be deposited and the substrate.
If the substrate cannot be heated to high temperature, the deposition must be carried out using low-temperature technology.
If the coating to be deposited consists of a solid element (metal or graphite target), a physical process such as PVD is used. If the coating consists of a gas or liquid, a chemical process such as CVD or PACVD is used.
Do you have a question or a need?
Our teams dedicated to vacuum deposition and coating are at your service.
Contact usOur latest news
Read our news about vacuum deposits.