Depending on how often they're used, how they're laid out and the materials they're made of, metal parts can wear in a variety of ways. Corrosion, abrasion, adhesion or simply fatigue, each situation is treated differently. Heat treatment in the mass, case-hardening, nitriding: which process for which wear mode?
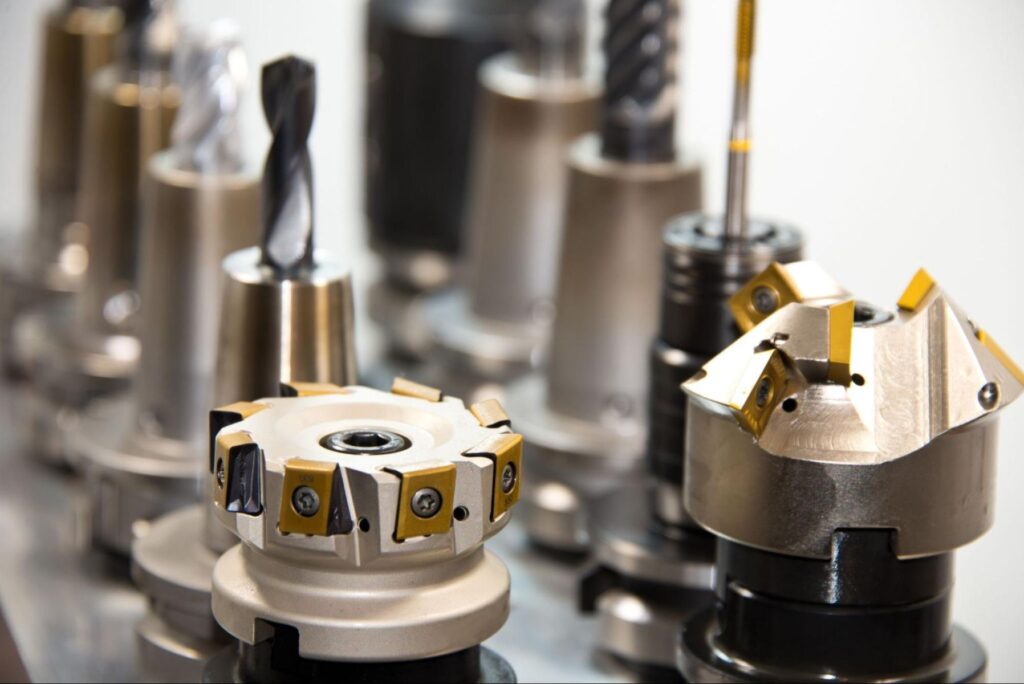
Different types of wear
Surface wear is a natural phenomenon in which the surface layers of a solid element are degraded. Yet there are as many ways to improve the durability of metal parts as there are to wear them. In fact, the process to be chosen for strengthening a component depends above all on the type of wear it is subjected to.
As a result of repeated stress over time, the part may experience natural fatigue and eventually break. Under certain conditions, the surfaces of certain components can also adhere to each other or pull particles apart, a process known as adhesive wear. On the other hand, when steel parts begin to "rust", we observe the phenomenon of corrosion. Finally, abrasive wear corresponds to friction between two surfaces, or a surface and a medium, during which hard particles of one impregnate or tear away the surface of the other, creating scratches or wear on the surface concerned.
The right solution for every wear phenomenon
Each type of wear operates in its own way, and requires appropriate treatment to preserve the metal parts concerned. Selecting a surface treatment therefore requires first and foremost determining the type of wear suffered.
Fatigue wear
Fatigue wear can occur on a metal part that is subjected to regular stresses, even if these sometimes appear to be quite low. Over time, cracks form on the surface of the component and propagate more or less rapidly. Treating this type of problem means preventing their development, or slowing it down if it becomes impossible to stop it completely. To achieve this, thermochemical surface treatments such as case-hardening or nitriding are used. In certain cases, for example when the part is subjected to significant mechanical stress right to the core of the material, it is possible to apply a heat treatment such as tempering.
Abrasive wear
In the case of abrasive wear, where hard particles on one surface eventually scratch the other, the aim is to reinforce the surface hardness of the parts. This is achieved by applying a vacuum coating such as PVD. To further enhance hardness, parts can also be nitrided.
Adhesive wear
Adhesive wear means that two moving parts, rubbing against each other, detach fragments of material from each other's surfaces and end up sticking or welding together. To combat this phenomenon, we need to act on the friction coefficient of the parts to limit the risk of seizure. In this situation, the most suitable surface treatment is a DLC coatingcoating, which significantly reduces this risk.
Corrosive wear
If the surface of a part shows signs of corrosive wear, it must be prevented from being completely degraded by oxidation. To prevent this, a post-oxidation nitriding treatment or a vacuum coating such as PVD or DLC is applied to improve the metal's resistance.
Special case of stainless steel
Stainless steel can also be subject to certain types of wear. However, the treatments to be applied differ: in the case of abrasive wear, a vacuum diffusion treatment such as Thermi SP is applied. If it shows signs of adhesive wear, on the other hand, it's best to opt for a Thermi DLC treatment.
Would you like to increase the durability and strength of your metal parts? Thermi-Lyon, specialists in vacuum treatment and nitrocarburizing for 50 years, can help you add value to your products.