Vapor deposition is one of the main coating processes used on metal parts. This method enables various modifications to be made to the material's properties: improved resistance to corrosion, wear and friction, changes in visual appearance, etc. Vapor deposition generates the accumulation of thin layers on the surface of a part, and can be carried out in two ways: chemically or physically.
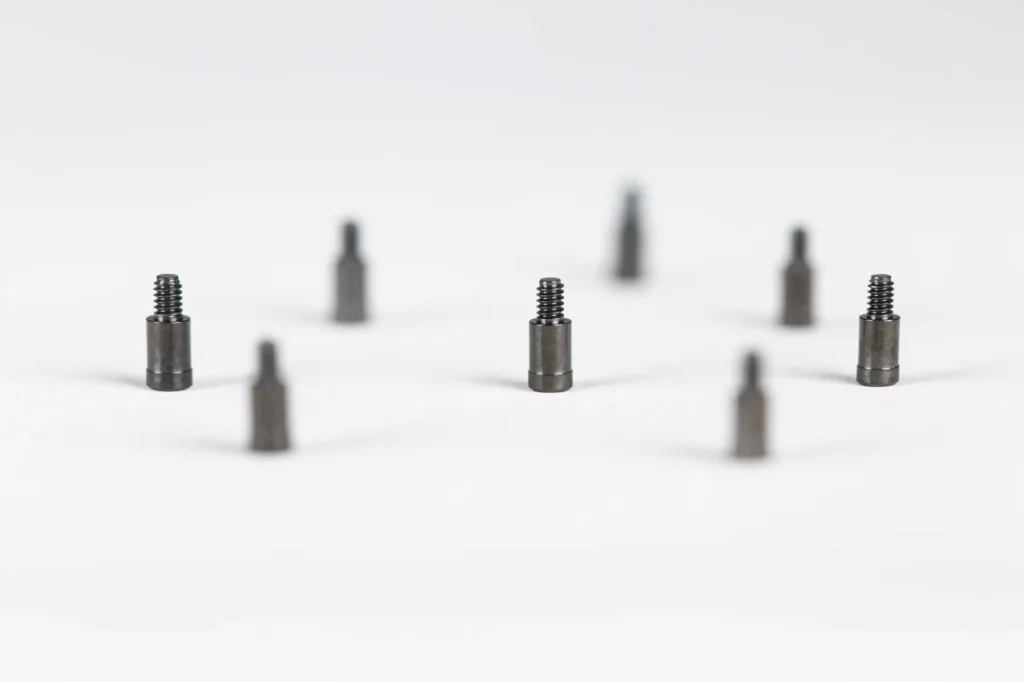
PVD, CVD: what are they?
Nowadays, most industrial metal parts undergo a surface treatment, essential for improving their machinability, corrosion resistance, wear resistance or even their optical or electrical properties. This operation involves vacuum deposition of several thin layers a few nanometers or micrometers thick on the surface of the part. These can be applied either chemically (CVD) or physically (PVD).
CVD, or Chemical Vapor Deposition, is applied at a temperature of between 800 and 1,000 degrees Celsius. It guarantees excellent results because it relies on a chemical reaction between the base substrate, the part surface and a volatile compound. These two elements react to form a solid material deposited on the surface of the part. This technique is widely used in the production of carbide extrusion dies, for example.
PVD, or Physical Vapor Deposition, is based on a physical process. It is applied at a much lower temperature, ranging from 200 to 450 degrees Celsius, and involves evaporating a source material under vacuum so that it deposits on the surface of a part. This method is used in particular on punches, cutting tools and dies.
2 criteria for choosing the right method
For the chemical reaction to take place and for the coatings to adhere properly to the part, the temperature of the environment remains crucial, as does the geometry of the part to be coated.
Required heating temperature
The first criterion to take into account is the temperature tolerated by the workpiece material. Some metals, such as carbides, tolerate heat very well, and are ideal candidates for chemical CVD treatment. The main advantage of this method remains the quality of the coating's adhesion, as well as the speed of the process. On the other hand, some materials, such as aluminum, cannot be treated at too high a temperature, otherwise they will melt. In this case, it's best to opt for a PVD process. To choose the right coating process, you need to take into account the temperature required by the method (CVD or PVD), and the material's tolerance under such conditions.
Part geometry
In addition to temperature, the geometry of the part must also be monitored. While the PVD method is perfectly suited to the surface of many metal parts, it may prove ineffective in certain cases. For example, if the part has too small holes, just a few millimeters deep, a PVD treatment may not be enough to fill them. If the base material cannot withstand high temperatures, CVD is not an option, and you may find yourself at a dead end. Fortunately, a new system has been developed to counter this phenomenon.
PA-CVD, a hybrid technique
Thermi-Lyon now uses the PACVD process to provide the best possible treatment for parts that cannot withstand high temperatures and require optimum coating. Combining the two methods, this technique triggers the desired chemical reactions at lower temperatures. This hybrid system enables chemical vapor deposition at temperatures between 150 and 200 degrees, and is used by Thermi-Lyon for its Thermi DLC and Thermi-platin coatings.
Thermi-Lyon has recognized know-how in heat treatment for all types of metal parts.
All about the CVD process
How does the CVD process work?
The CVD or " Chemical Vapor Deposition " process consists, as its name suggests, in depositing a thin layer of solid material on a substrate by means of a chemical vapor reaction. A mixture of reactive gases is then injected into the reactor to interact with the surface of the part under very specific temperature and pressure conditions. This method produces a uniform coating, even on complex shapes.
What are the areas of application for CVD?
The CVD process is used to deposit thin films of silicon carbide(SiC), silicon nitride(Si3N4) and gallium nitride(GaN) on substrates in the manufacture of materials for semiconductors, light-emitting diodes(LEDs) and lasers. Particularly in the electronics sector, these films enable controlled component growth and exceptional uniformity.
In solar energy, CVD is used to create coatings on photovoltaic cells via the chemical deposition of amorphous silicon or zinc oxide(ZnO), thus improving photovoltaic conversion and energy efficiency.
CVD offers coatings resistant to extreme conditions, such as tungsten carbide, carbon, or titanium nitride (TiN), used to increase the durability of mechanical parts, cutting tools, and molds in theindustrial environment.
This process is also crucial in the manufacture of functional materials for MEMS (micro-electro-mechanical systems), such as polysilicon and silicon nitride, enabling miniaturization and the development of high-performance micro-systems.
The advantages of CVD
The CVD process process produces high-purity solid films, essential for applications such as semiconductors andepitaxy. It offers great flexibility, enabling the deposition of a variety of materials, such as carbon, tungsten or silicon carbide, making the process applicable to sectors such aselectronics,automotive and specialized coatings. Thanks to precise control of gaseous reaction conditions and parameters such as temperature and pressure, it guarantees continuous, homogeneous growth of thin films even under high pressure. CVD also enables the formation ofalloys suited to extreme environments, while meeting the needs of high-speed, high-volume production .
Disadvantages of the CVD process
Unfortunately, this process CVD process generates hazardous by-products (toxic, corrosive or explosive), requiring costly health and environmental safeguards. Thermal processes create stresses on substrates, particularly when materials have different coefficients of expansion. In addition, precursor gases, such as those used in the production of diamond or graphene, are often quite expensive, adding to the overall cost of the process.
Finally, theequipment required for CVD, notably plasma or hot filamentThis may limit access to this technology for companies with limited budgets.