Bonded coatings are an excellent way of improving the coefficient of friction of metal parts. Applied, possibly following a heat-treatment operation, it ensures that the parts slide better together and reduces the risk of seizing. This technology is particularly useful in the construction and screw industries, but also in everyday life, as it can be found in most kitchens, in a well-known form!
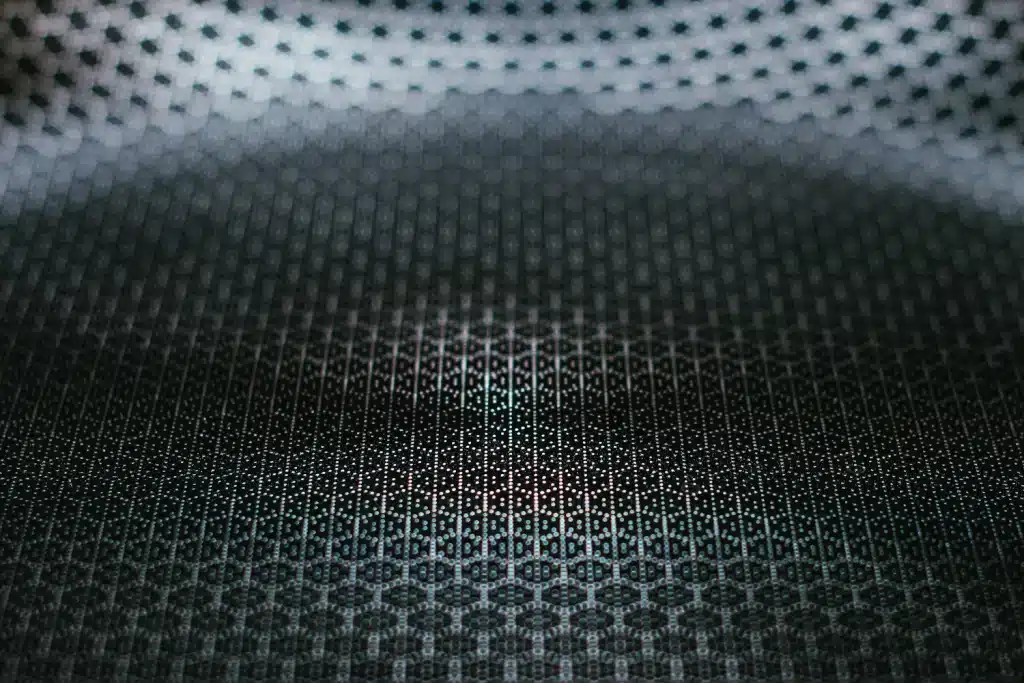
What is slip varnish?
As the name implies, the main purpose of a bonded coating is to improve the coefficient of friction of metal parts that have to work against each other. It is an additional layer applied to the surface following a heat treatment such as nitrocarburizing. One technique is to modify the heat-treatment parameters to obtain a more porous surface, which ensures better varnish adhesion. In fact, the more porous the surface layer, the longer the glide varnish is effective.
Most of the time, this consists of Teflon or molybdenum disulphide, two chemical elements with excellent sliding properties. The choice of varnish to apply to a part depends on the pressure applied to its surface as it works. Contrary to popular belief, however, slip varnish is a solid solution in the sense that, once polymerized, it forms a self-lubricating protective layer and no longer requires greasing or oiling to maintain parts.
A solution that gives treated parts new properties
Like the application of a specific paint to the surface of a metal part, the addition of a Bonded Coating modifies the natural properties of steel. Improving the coefficient of friction is, of course, the main objective of this method, but the glide varnish, also known as an antifriction coating, also reinforces the resistance of parts to corrosion.
Examples of glide varnish applications
This solution is widely used in the construction industry. It is, for example, a highly effective method for dealing with the locking systems on the masts of site cranes or aerial work platforms. Operating on metal axles that fit into and slide through the joints, these items of construction equipment can remain in place for quite long periods, ranging from a few weeks to a few years. The prior application of a sliding varnish is therefore an ideal solution to prevent the locking systems from seizing up over time. Since the varnish is self-lubricating, there's no need for dangerous greasing operations at heights of several meters. Combined with a nitrocarburizing treatment, this technique guarantees improved resistance to wear, corrosion and friction.
Slip varnish is also used in the kitchen, in pots and pans, to prevent food from sticking during cooking.
DLC as an alternative to glide varnish
The application of a glide varnish complements a heat treatment operation, usually nitrocarburizing, to further enhance the strength of the parts. While this method may seem ideal for making components more resistant to friction, it does have its limitations, and in some cases proves complex to implement. In fact, some products contain eternal pollutants, PFAS, which remain very stable over time and cause considerable environmental damage.
Ever mindful of the need to protect the planet, the Thermilyon group has come up with an alternative solution to the use of glide varnish, and has developed a vacuum coating that is also self-lubricating: DLC, Diamond Like Carbon. DLC, Diamond Like Carbon. Vacuum technologies are currently the most environmentally-friendly, as they emit no CO2 and require no gas or polluting resources, only electricity. What's more, DLC is biocompatible, i.e. it does not affect the human organism when it comes into contact with it. This aspect is particularly important in fields such as medical, food or even cooking, as mentioned above. DLC offers an eco-friendly alternative to glide varnishes, durably improving their coefficient of friction as well as their resistance to corrosion and wear. The replacement of these varnishes by vacuum treatment is convincing more and more customers, as the Thermilyon Group processes more and more components each year using this process.
Slip varnishes are widely used in the building and civil engineering sector, where they provide screws and bolts, and the masts of construction cranes and aerial platforms with excellent frictional properties. Made from Teflon or molybdenum disulphide, they can be applied in addition to heat treatments such as nitrocarburizing, and have the advantage of being self-lubricating. Nevertheless, some of these products contain eternal pollutants that are harmful to the environment, which is why the Thermilyon Group has developed a vacuum treatment solution that guarantees the same properties for parts, but without CO2 emissions or complex chemical elements: DLC. This environmentally-friendly solution makes parts naturally more resistant to wear and corrosion, and requires no subsequent maintenance or lubrication.