Vacuum deposition is one of the technologies of the present and future - carbon-free, non-polluting and extremely efficient. In line with its commitment to offering the most appropriate solution for its customers' needs, Thermi Lyon has developed two coatings offering excellent resistance to wear, abrasion and corrosion: DLC and CrN. These two technologies complement each other to produce protective coatings. Historically produced at the Lyon site, THERMI-DLC can be produced in two ways: by PACVD or PVD Magnetron.
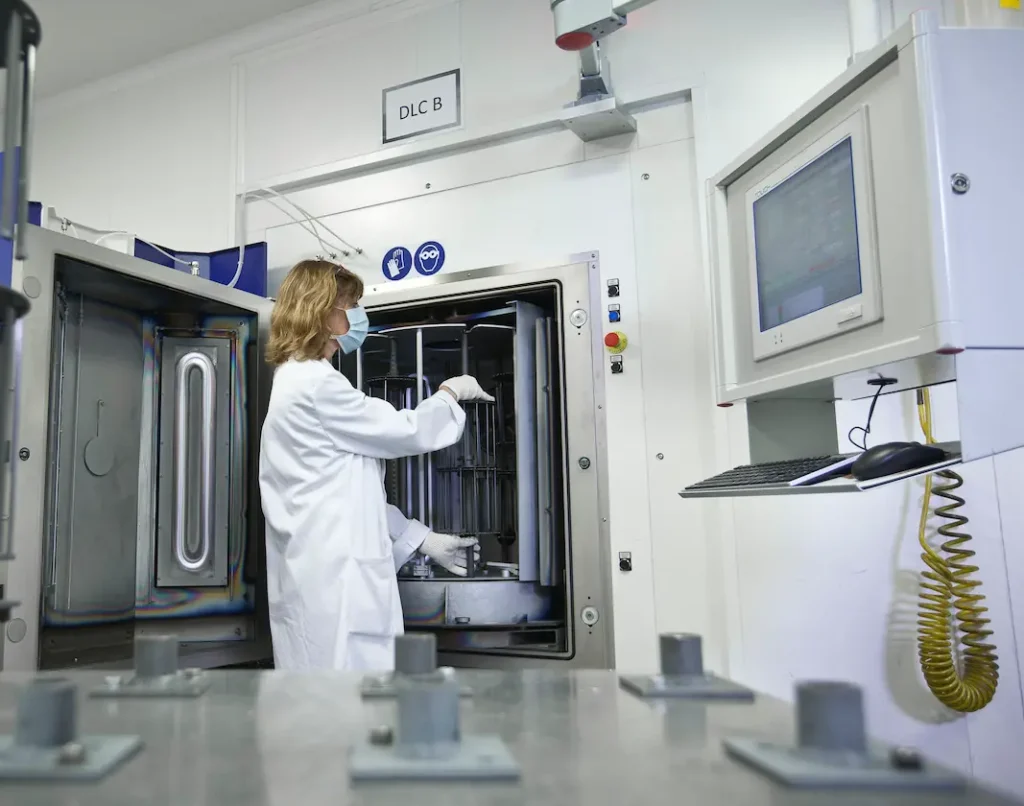
DLC and CrN, two versatile solutions with multiple benefits
DLC and CrN coatings are vacuum technologies that can be applied to a wide range of materials , including steels, stainless steels, copper-based metals, titanium and carbides. Both solutions offer numerous advantages, starting with their biocompatibility (in the case of DLC) and their production method, which is far more environmentally friendly than that of hard chromium, for example.
What is DLC, Diamond Like Carbon?
The DLC (Diamond Like Carbon) coating developed by Thermi-Lyon offers exceptional resistance to wear and, above all, to seizure. It has a very low coefficient of friction and a hardness of between 1,500 and 2,500 HV, making it an ideal technology for materials subject to high levels of wear and friction. As a result, it is widely used, for example, in the automotive sector, particularly in Formula 1 racing, but also in the aerospace industry.
DLC is also a biocompatible solution, i.e. it does not affect the human organism when it comes into contact with it, which is why it is particularly appreciated by health and food professionals. In addition to these properties, this coating is highly resistant to corrosion. Integrating parts coated with this type of technology considerably reduces the need for oiling and lubrication in a system. Over the long term, DLC offers real savings in terms of lubrication and maintenance.
Focus on CrN, chromium nitride
Chromium nitride, CrN, also boasts a very attractive hardness of over 1,800 HV. Twice as hard as hard hexavalent chromium, this coating represents a highly effective alternative to this technology, the production of which remains subject to very strict regulations. What's more, CrN offers excellent resistance to corrosion and abrasion.
Two complementary vacuum production technologies
Both DLC and CrN coatings belong to the family of vacuum technologies, which are versatile and less polluting than traditional treatment methods. DLC can be produced in two ways: PACVD or PVD. In many cases, the advantages of one make up for the limitations of the other, which is why Thermi Lyon has mastered both methods in order to respond ever more precisely to its customers' needs. THERMI-LYON has also developed its own PVD Magnetron treatment technology.
PACVD, Plasma Assisted Chemical Vapor Deposition
PACVD treatment is based on a chemical reaction, assisted by electrical energy forming a plasma. The DLC layer is produced by a chemical reaction with C2H2 acetylene. The result is a deposit of solid carbon and hydrogen forming an amorphous layer. The temperature does not exceed 250°C, and the result is a layer with significant tribological properties.
This method gives us total control over surface roughness, and avoids the degradation caused by the droplet spraying familiar from PVD. In fact, it can be applied to finished parts, which really saves time. On the other hand, as detailed above, PACVD induces the presence of hydrogen in the protective layers, which can generate a certain chemical instability in the coating. So, if the treated part has to work in a medium such as water or a liquid, for example, the structure of the DLC layer can change and delaminate more easily.
PVD, Physical Vapor Deposition
PVD, or Physical Vapor Deposition, is an entirely physical vacuum deposition process, as the name suggests. Thermi-Lyon has developed its own process based on this technology, using the Magnetron principle. This involves creating a vapor of the material to be deposited by combining plasma and magnetic energy. This technology can be used to produce tribological layers for anti-seize applications such as DLC coatings. The absence of hydrogen in DLC coatings produced by PVD ensures better chemical stability of the coating, and in some cases, better adhesion than coatings produced by PACVD. Nevertheless, unlike the previous technique, a PVD treatment can slightly degrade the surface roughness of certain parts. It remains, for example, very difficult to treat aluminum with PVD, whereas it is perfectly possible to do so with PACVD. The two technologies therefore seem to complement each other, offering a viable solution to every problem.
Applications for DLC and CrN deposits
DLC and CrN vacuum coatings are extremely versatile, thanks to their many properties. As they make materials significantly more resistant to wear, abrasion and corrosion, and seizure in the case of DLC, they are widely used in sectors such as aerospace, automotive, special machinery or even sports and leisure, as they are ideally suited to moving parts. The absence of any need for greasing or oiling makes DLC particularly interesting in this respect.
CrN's good resistance to wear and corrosion makes it a green-tech alternative to hard chrome plating.
Vacuum deposits like DLC are also biocompatible, making them ideal for use by healthcare professionals in the design of dental prostheses and ancillaries, for example. It is also Food & Drug Administration-approved, which is invaluable to the food industry, where it can be applied, for example, to mincer grids, bottling equipment, conveyor systems and other special machines. These treatments have been carried out at Thermi-Lyon's historic site in Lyon for some twenty years.