Plasma-assisted low-pressure carburizing, also known as ion carburizing, is a heat treatment based on carbon diffusion. This method is used to reinforce the wear resistance of materials, and above all, it uses vacuum technology. Developed in France by the Thermilyon group in the 1990s, this technology can treat only certain well-defined zones, thanks to the use of metal covers. Its development took place over several years, and went through many twists and turns.
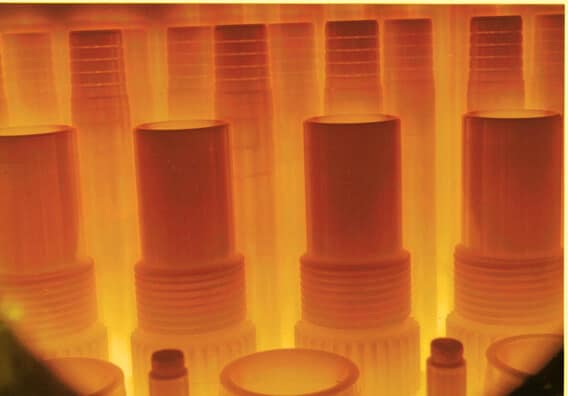
Where does ion carburizing come from?
Plasma-assisted low-pressure carburizing is based on the diffusion of carbon atoms on the surface of parts, to enhance their wear resistance. This treatment offers a number of advantages: clean, environmentally sustainable vacuum treatment, uniformity, no risk of internal oxidation, and, as with ion nitriding, plasma spares certain areas that should not be case-hardened.
In fact, there are two types of vacuum carburizing: low-pressure carburizing and plasma-assisted low-pressure carburizing, also known as ionic carburizing. In the 1990s, the Thermilyon group became a true pioneer of ionic carburizing in France, where the process did not yet exist. At the time, the company was offering case-hardening to a wide range of customers in a variety of sectors. However, many of them, notably automotive professionals, did not need to treat the whole part, but only certain well-defined parts. Unfortunately, the technologies available to carry out this type of processing at the time are quite time-consuming and costly. Indeed, before the advent of the plasma method, partial carburizing required the application of a special paint to the areas to be preserved. This product remains quite expensive and, during treatment, releases chemicals that disturb the atmosphere, leading to non-conforming parts.
Engineers at Thermil Lyon came up with a more practical and viable solution, based on ion nitriding. This method relies on the use of covers, not paint, and has proved highly effective. This is how ionic carburizing came into being.
Thermi-Lyon, national pioneer in plasma-assisted carburizing
Plasma-assisted low-pressure carburizing delivers excellent results. The materials are vacuum-treated, ensuring clean parts with little deformation and excellent mechanical strength. The process developed by Thermi-Lyon has even been validated by major international automotive equipment manufacturers. One problem remains, however: the productivity of this process is insufficient to achieve the target prices sought.
From plasma-assisted carburizing to low-pressure carburizing
The group's researchers therefore decided to modify the process in order to adapt it to this need, and developed low-pressure carburizing. In this first version of the treatment, the carbon reaches the parts by means of propane gas diffusion. Cheaper and more practical than basic ionic carburizing, this technique produced excellent results and enabled Thermi-Lyon to win new customers. However, a new obstacle has arisen: over time, the propane also reacts with the cold parts of the parts, forming elements that clog the injectors of the treatment furnaces (soot, tar, etc.).
The Group's engineers discover that scientists have developed a version of low-pressure carburizing that diffuses carbon not with propane, but withacetylene. This gas reacts preferentially on hot parts. This technique has none of the problems associated with propane, and generates no soot.
As a result, plasma-assisted carburizing gradually gave way to the low-pressure version. Today, however, it is still possible to protect parts from heat treatment using the copper plating method. This involves depositing copper on the parts to be protected, to prevent carbon from penetrating. Complex and costly, this technique requires an initial electrolytic treatment and subsequent removal of the copper, but it remains the method certified by aeronautics professionals, for example. So there are many ways to case-harden parts while adapting to their geometry, something the Thermilyon group has been doing for over sixty years.
Although the Thermilyon group no longer offers plasma-assisted carburizing to its customers, it has developed this process in France, and is therefore able to call on it should the need arise.