La nitruration gazeuse constitue un procédé de traitement thermique à base d’azote. Cette technique a vu le jour au début du siècle dernier dans le milieu de l’armement et s’emploie aujourd’hui dans de multiples secteurs d’activités industriels. En raison de sa très basse température de mise en œuvre et des nombreuses propriétés qu’il confère aux pièces, ce traitement semble particulièrement intéressant et durable, et se décline en différentes technologies.
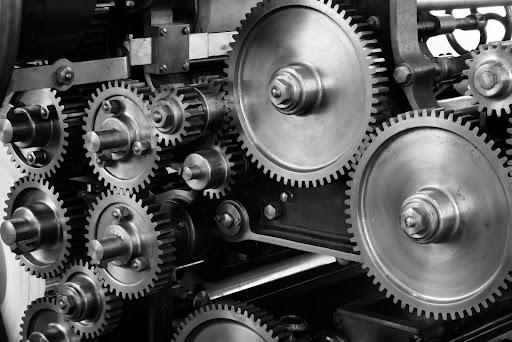
Origines de la nitruration
Le terme « nitruration » vient en réalité du nom anglais désignant l’élément azote, « nitrogen ». Noté N dans le tableau périodique des éléments, l’azote se trouve donc à la base du traitement par nitruration. Son utilisation a émergé dans les années 1910 aux États-Unis et en Allemagne, développée par les industriels de l’armement.
Avant cette invention, ces fabricants rencontraient un problème de taille : les traitements employés jusqu’alors se déroulaient à haute température et modifiaient la structure des tubes à canon, qui se voyaient automatiquement déformés. La nitruration gazeuse permettait alors de traiter l’intérieur de ces tubes tout en préservant leur forme.
Ce procédé représente ainsi l’un des premiers traitements basse température utilisés dans l’industrie à des fins de durcissement. Cette méthode offre la possibilité de traiter facilement les alésages des pièces mécaniques tout en suscitant très peu de déformations. Suite aux essais prometteurs de cette technologie sur les tubes à canon, la nitruration gazeuse s’est peu à peu répandue jusqu’à devenir une technique habituelle de traitement thermique des métaux.
Comment fonctionne la nitruration gazeuse ?
La nitruration gazeuse repose sur une réaction chimique simple, qui consiste à décomposer un gaz, l’ammoniac. Celui-ci se compose d’un atome d’azote et de trois atomes d’hydrogène, sa décomposition engendre ainsi une diffusion d’azote dans l’atmosphère.
Avantages de cette technologie
Le premier avantage reconnu à la nitruration gazeuse reste la faible température de mise en œuvre qu’elle nécessite. Au lieu des 1000 degrés Celsius de la cémentation ou de la trempe, cette réaction chimique peut se dérouler à seulement 500 degrés Celsius, ce qui garantit une meilleure maîtrise dimensionnelle de la pièce traitée.
Par ailleurs, la nitruration gazeuse d’un acier génère la formation de nitrures de fer de chrome, de vanadium ou d’aluminium selon la composition chimique de l’acier. Ces derniers participent à renforcer la résistance de la pièce à l’usure de manière considérable. La formation de cette couche nitrurée peut se décomposer en deux : la couche de combinaison, qui se trouve à l’extrême surface de la pièce et la couche de diffusion, qui se crée sur quelques dixièmes de millimètres de profondeur. La première affiche une dureté exceptionnelle, supérieure à 1000 Vickers et s’étend sur quelques microns de profondeur. Elle apporte à la pièce une excellente résistance à l’usure et un très bon coefficient de frottement. La couche de diffusion correspond, comme son nom le laisse entendre, à la zone où l’azote se diffuse et peut aller jusqu’à un millimètre de profondeur sous la surface de la pièce. Cette couche sert notamment à améliorer la résistance de la pièce à la fatigue.La nitruration gazeuse fait partie des traitements thermiques multipropriétés, car il s’agit en réalité d’une méthode particulièrement polyvalente. Il est possible d’ajouter, dans certains cas, une étape de diffusion d’oxygène. On parle alors de post-oxydation, un procédé qui contribue à renforcer la résistance à la corrosion des pièces. Enfin, ce traitement présente aussi l’avantage de s’appliquer sur des pièces finies, c’est-à-dire qu’une fois traitées, elles ne nécessitent pas de reprise d’usinage. La nitruration gazeuse peut donc engendrer un réel gain de temps et d’argent. Il est également possible de faire diffuser en même temps que l’azote du carbone. On parle alors de nitrocarburation, traitement avantageux car il peut s’appliquer sur des aciers moins alliés donc moins coûteux.
Limites de la nitruration gazeuse
La cinétique de traitement constitue sans doute la principale limite de cette solution. En effet, le temps nécessaire au bon déroulement du processus peut paraître très long. En fonction de l’acier composant la pièce, un traitement par nitruration gazeuse allant jusqu’à 1 mm de profondeur peut durer une centaine d’heures, contre seulement 10 heures dans le cas d’une cémentation. De plus, la performance finale de la nitruration dépend aussi de la nuance d’acier traitée et de la quantité d’éléments d’addition dans l’acier permettant la formation de nitrures.
Diverses technique de nitruration gazeuse
Fidèle à sa volonté de proposer des solutions adaptées à tous les besoins, Thermi-Lyon propose trois techniques différentes de nitruration gazeuse : à pression atmosphérique, à basse pression ou à haute pression. La première se révèle particulièrement utile dans le milieu de l’aéronautique, par exemple, notamment pour traiter les paliers de moteurs d’avion. Ceux-ci ont besoin d’un traitement appliqué à plus d’un millimètre de profondeur, ce que la nitruration gazeuse à pression atmosphérique offre naturellement. Enfin, la solution à basse pression se déroule sous vide.
La nitruration gazeuse s’emploie aujourd’hui dans une vaste quantité d’industries : elle sert notamment à traiter les moules à injection de plastique ainsi que les outillages de mise en forme ou encore les pièces de turbochargeurs, les systèmes d’injection pour les moteurs automobiles et les soupapes de voitures. En raison de la facilité de sa mise en œuvre, ce traitement s’utilise dans presque tous les secteurs industriels, allant de l’automobile aux machines agroalimentaires.
Développée il y a plus d’un siècle par les industriels de l’armement, la nitruration gazeuse s’emploie aujourd’hui dans de nombreux secteurs, car elle offre une réelle facilité de mise en œuvre. Se déroulant à basse température, elle repose sur la formation de nitrures à la surface des pièces en acier grâce à la diffusion d’azote, ce qui confère aux pièces traitées une excellente résistance à l’usure.